Printing process and related equipment introduction
2021-08-14(599)Views
The process of printing patterns on textiles with dyes or pigments. Printing is divided into textile printing, wool top printing and yarn printing, and mainly textile printing. Top printing is used to make mixed-color tweed; yarn printing is used to weave special-style colorful pattern fabrics. Fabric printing has a long history. In the Warring States Period, China had already used hollow printing (see History of Dyeing and Finishing in China). India had printed wood stencils in the 4th century BC. Continuous gravure cylinder printing began in the 18th century (see Cylinder Printing). Screen printing is developed from the hollow pattern, which is suitable for small batch and multi-variety printing of easily deformed fabrics. In the 1960s, metal seamless rotary screen printing began to be applied, which provided conditions for continuous production, and its efficiency was higher than flat screen printing.
In the late 1960s, the transfer printing method appeared. Using the sublimation characteristics of disperse dyes, the dye on the transfer paper was transferred to synthetic fiber fabrics such as polyester by heating, and fine patterns could be printed. In the 1970s, a liquid jet printing method controlled by an electronic computer program was also developed. Many combinations of jet nozzles intermittently spray each color dye solution to form a colorful pattern, which is mainly used for carpet printing.
Process: Printed fabric is an artistic product, and the corresponding printing process is selected according to the design pattern. There are three commonly used direct printing, anti-dye printing and discharge printing. Direct printing is to directly print dyes or pigments on white or light-colored fabrics, and then after steaming and other post-processing to obtain patterns, the process is short and the most widely used. Anti-dye printing is a substance printed on the fabric to prevent dyeing or color development of the dye, and then dyeing or coloring, so as to obtain a pattern on the dyed fabric. Discharge printing is a printing process that prints on dyed fabrics to eliminate dyes and obtain patterns on dyed fabrics.
Dyes and pastes: The fabric must be pre-treated before printing to make it have good wettability. The dyes used in printing are basically the same as dyeing, and some smaller patterns can use paint (pigment). In addition, there are dyes such as fast pigments, fast amines, and fast sulfonates for printing. Different types of dyes can be used to print patterns in various colors on the same fabric. When printing, the dyes or pigments are mixed into color pastes. After printing and drying, it is usually steamed, developed or fixed, and then soaped and washed to fully remove the paste, chemicals and floating color in the color paste.
The printing paste is composed of dyes (or pigments), moisture absorbents, co-solvents, etc. and the original paste. The function of the original printing paste is to make the color paste have a certain viscosity and fluidity. It is made of hydrophilic polymer paste. Commonly used pastes include starch, starch degradation products (white dextrin and yellow dextrin), starch ether derivatives, sodium alginate (or ammonium), hydroxyethyl Honey locust gum, dragon gum, cellulose ether, synthetic polymer electrolyte, etc. The emulsified paste made with water, kerosene and emulsifier is sometimes used as the original printing paste. The original printing paste should have good stability to the chemical agents in the color paste, does not interact with the dye, has a certain adhesion to the fiber and is easy to wash off the fabric. The viscosity of the printing paste is determined by the nature of the original paste. When printing, if the viscosity of the color paste drops too much, it will be difficult to print fine lines, and if the viscosity is too large, the color paste will not easily pass through the pores of the screen.
Steaming and its equipment: Steaming is also called steaming. The fabric printed with the color paste is dried and then steamed. The steam condenses on the fabric, causing the temperature of the fabric to rise, the fibers and pastes to swell, and the dye to dissolve and dye up. Some dyes also undergo chemical reactions during the steaming process. Due to the existence of the paste, the dyeing process of printing dyes is more complicated, and the steaming time is longer than the steaming time of pad dyeing.
Latest News
-
Knowledge of T-shirt printing machine
T-shirt printing machine refers to a digital full-color prin...
-
Maintenance skills of digital printing machine
If a worker wants to do his job well, he must first sharpen ...
-
How to maintain the digital printing machine
Since the development of the digital printing industry, grea...
-
What is the difference between digital printing machine and traditional printing machine
In recent years, digital printing machines have become popul...
Contact Us
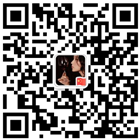
24-hour service phone18617068102
—— Communicate directly with WeChat
-
Advisory
Online Service -
Follow us
18617068102